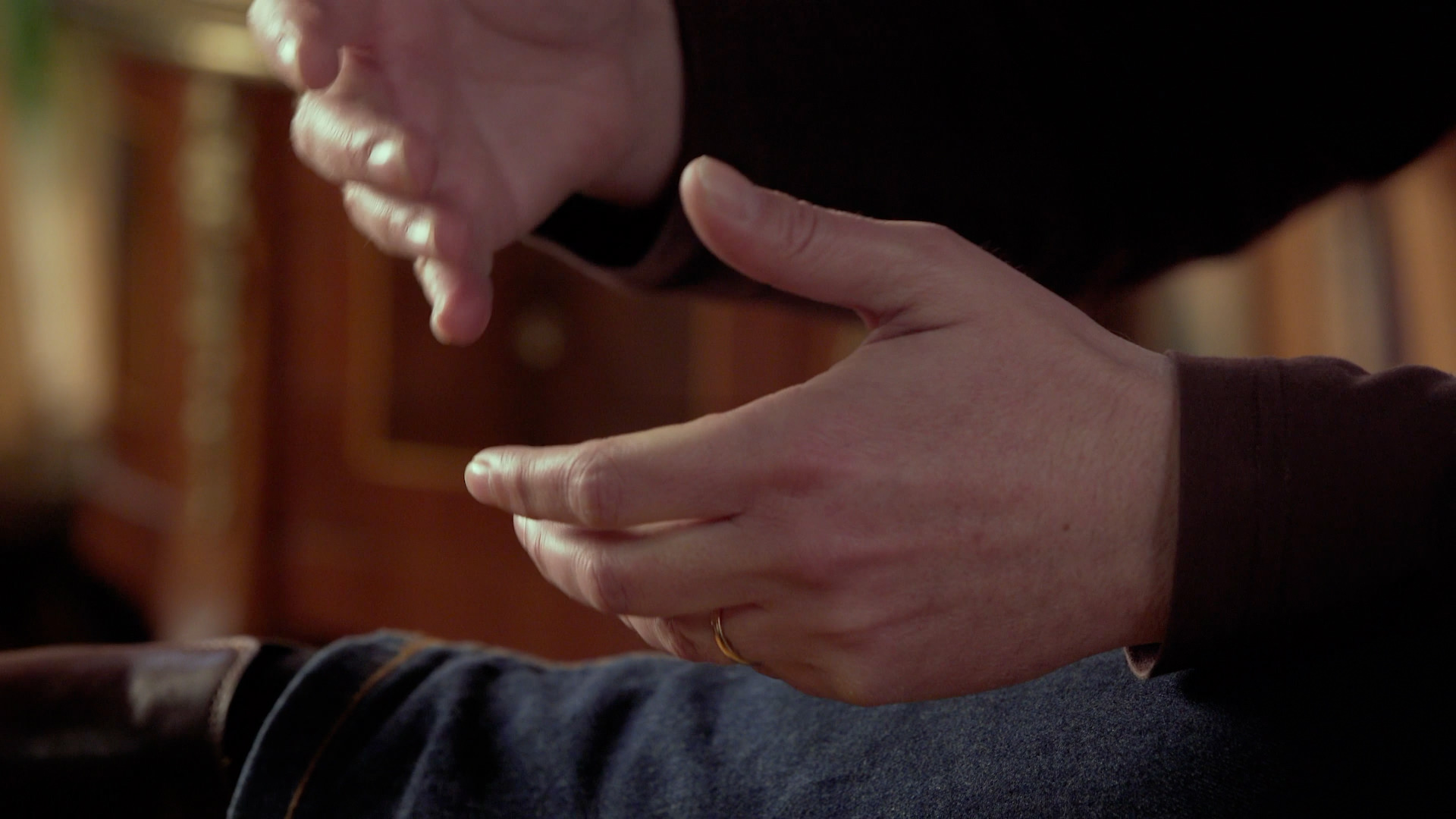
We asked Tamagawa Microtep Co., Ltd., who realize products “that it would be good to have” in the world with their great overall strength, about their feelings using Tokyo Seimitsu-manufactured measuring machines and their challenges going forward.
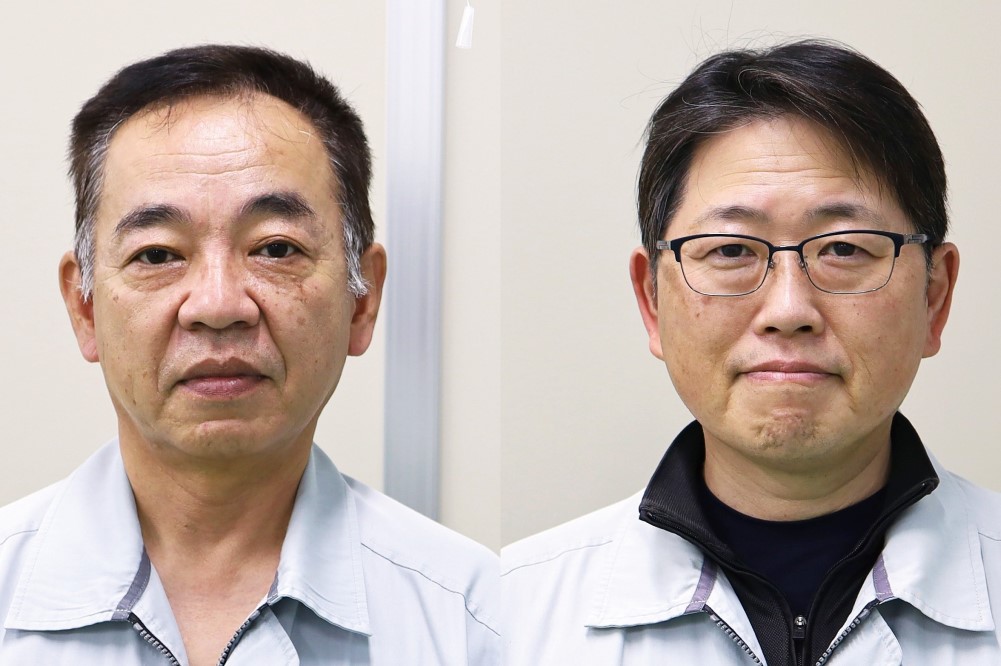
Tamagawa Microtep Co., Ltd.
General Manager 2nd Manufacturing Dept. Mr. Tomoo Shirota
Detection Gear Machining Section 2nd Manufacturing Dept. Mr. Hiroshi Kanayama
【Company Profile】
The company was established when 3 companies merged into a manufacturing business under Tamagawa Seiki Co., Ltd. in 2011. Through integrated production from equipment design to processing and assembly, they have achieved centralization of quality control and short delivery times.
Following the wish of the founder of the parent company, Tamagawa Seiki, to “secure manufacturing and employment in the hometown,” the business expanded into Iida, Nagano Prefecture. In 2014, the company won the “Nagano Prefecture Labor Statistics Survey Excellent Operation Site Commendation.”
As well as making products that delight customers, they strive to contribute to the local community.
Headquarters
1020 Kega, Iida, Nagano Prefecture 395-0813 Japan
Kamisato Plant
586-10 Kamisatobeppu, Iida, Nagano Prefecture 395-0003 Japan
Ohyasumi Plant
1879 Ohyasumi, Iida, Nagano Prefecture 395-8515 Japan
First of all please tell us the details of your company’s business.
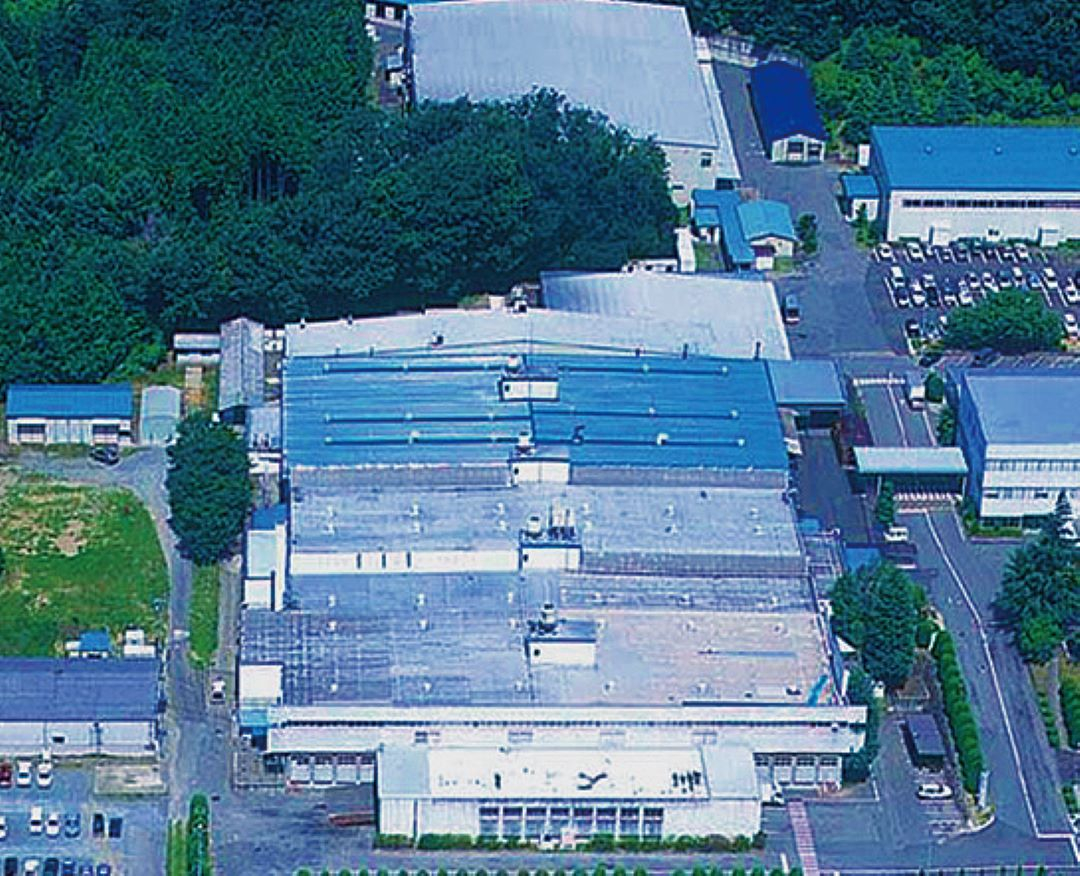
Tamagawa Microtep is a 100% subsidiary of Tamagawa Seiki. The company was established in 2011 from the merger of Kamtep, Misayama Microtep, and Remcast, and later Tamagawa Aviation Electronics and Tamagawa Aviation Electronic Devices merged with the company to become the current Tamagawa Microtep.
Even among numerous subsidiaries our company is somewhat special in that we deal with parts for transport in general, namely automobiles, trains, and planes.
Businesses that manufacture parts for all of these are quite rare, right?
In addition, we manufacture step motors for amusement rides, for example.
What are the proportions of the businesses?
The Automotive Equipment Manufacturing Business is around 40%.
In terms of worldwide share, 70% of hybrid vehicles contain Tamagawa Seiki Group’s sensors. For Toyota alone, that becomes almost 100%.
In railways, too, as well as sensors for detecting speed, sensors for detecting properties such as the tilt of the car body or the temperature of the axle are also used.
The next highest proportion to the automobile business is the Civil Aircraft Device Manufacturing Business which is about 20% of business. We have integrated from parts processing to assembly for products such as sensors and motors.
Originally, Tamagawa Seiki was a defense industry manufacturer. At first, we made the oil pressure meters for fighter planes, for example, but later we applied that technology and shifted to businesses to meet private sector demand.
Maybe you have heard of this for automobiles, but a system called the “by-wire system” is installed in planes, and our sensors are important parts in that system. The pilot’s operation is converted into an electrical signal, that is read by a sensor that measures the rudder angle, the acceleration, and the brake angle, and so the aircraft can be controlled.
This area is a specialist field of Tamagawa Seiki Group.
When using Tokyo Seimitsu`s measuring machines, how have you found them?
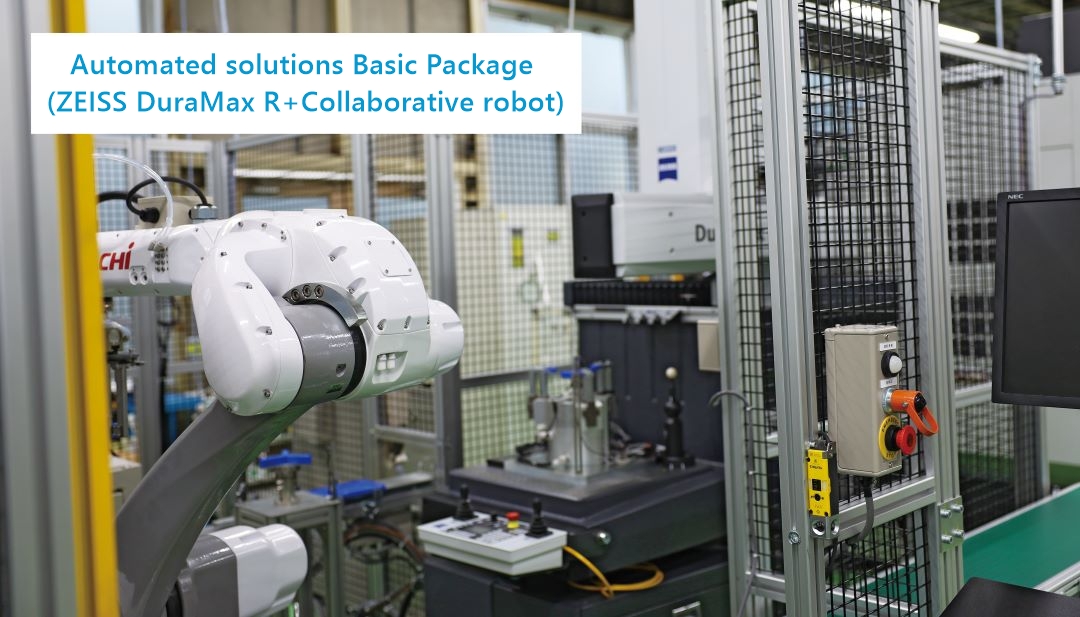
(ZEISS DuraMax ®+Collaborative robot)
The surface texture measuring instrument used in our detection gear is Tokyo Seimitsu’s HANDYSURF+. We have used it without any malfunction or trouble.
However, this time we are actually using Tokyo Seimitsu’s coordinate measuring machine for the first time. Not only this time, but regarding replacement of measuring machines made by other companies, it seems there is also a difficult aspect from the on-site viewpoint.
It would be good if there were something like an automatic conversion tool for the program.
Could you tell me your reasons for selecting the automated solutions Basic Package ZEISS DuraMax®?
It is easy to program.
Also, it can be used easily on-site, not just in the inspection room, which is a great benefit for the on-site people. This was possible only with the Tokyo Seimitsu product.
Talking about the ease of use aspect, there are other measuring machines made by other companies that are also easy to use, but if there is no traceability system as far as the source devices, then we cannot use them for aircraft-related work.
Tokyo Seimitsu: l’m blowing our own trumpet, but we have also proposed an aero solution targeting the aircraft market. We would be pleased if this were of help to you in the future.
What are your expectations of Tokyo Seimitsu going forward?
The area of maintenance. For example, the response when there has been a malfunction or when something has happened.
This is also the case for machines, equipment, and so on, but if a manufacturer is not very responsive even if we contact them, then we do not want to use them the next time. Not surprisingly, we want generous help in the service and support areas.
And another thing, in measuring functions in automated lines, even if they are not connected to heavy duty equipment, we want a system that can measure processed items from different lines as a single unit, and in 1 or 2 hours.
There was talk of the operating rate not being high at first, but we proposed manual measurement or installation of a robot.
Do you use collaborative robots at your company?
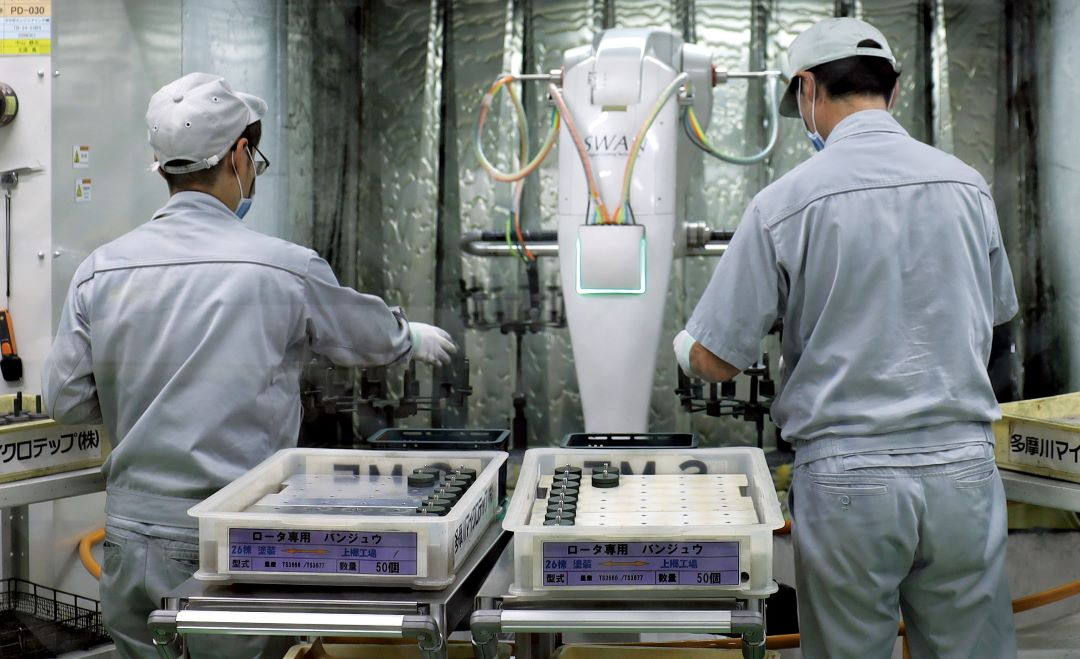
We have several. In another area, we operate robots for painting. Nowadays, human resource recruitment is becoming extremely difficult, so we are thinking that we want to actively introduce robots in lines where there is production volume.
I hear that solutions are difficult for automation of small-lot, high-variety processing.
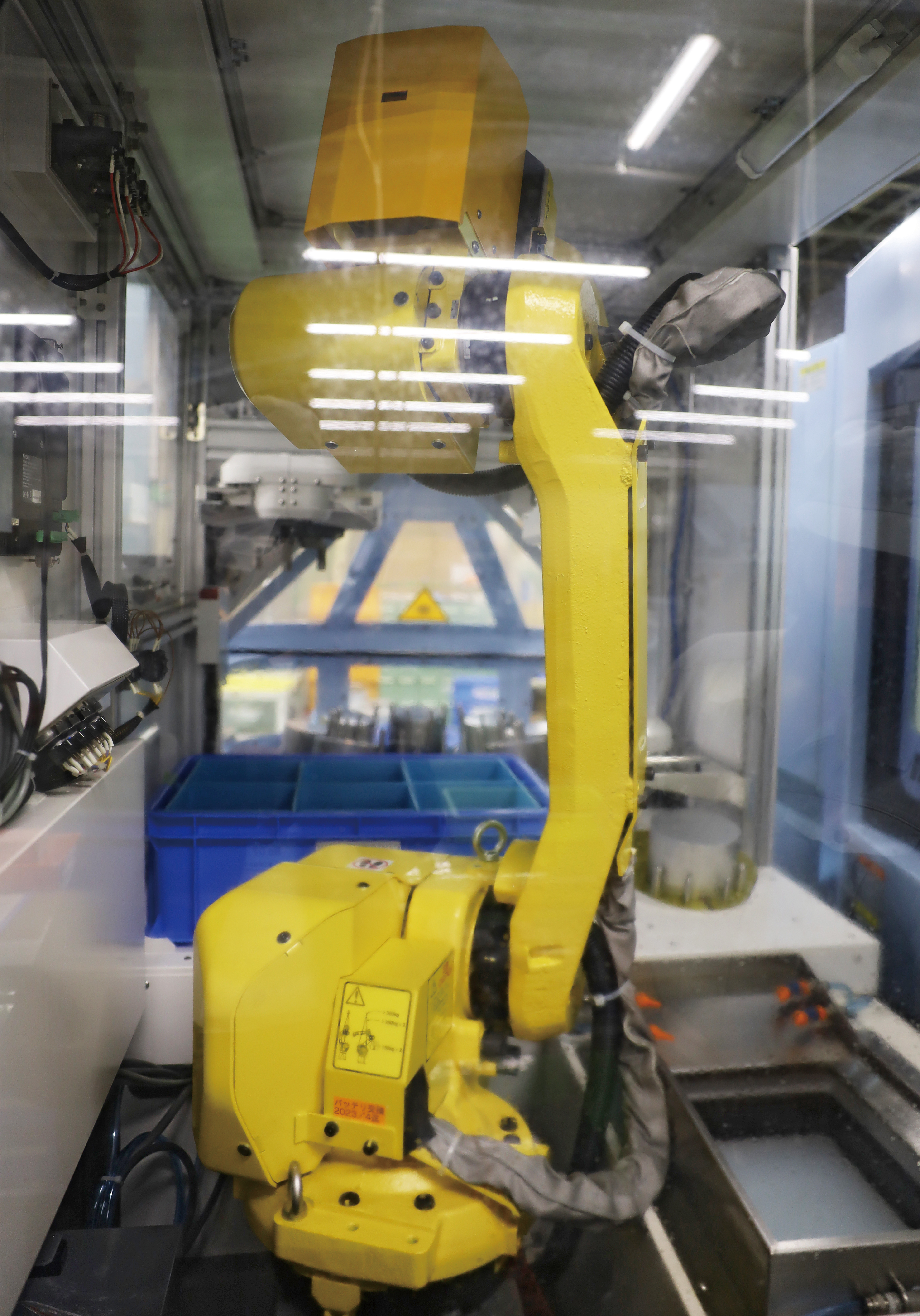
At our company we have processing machines with robots attached that stream items, and the setup time is shortened by, for example, automatically changing the claws that grasp the products.
Also, by making robots that are stopped for 70% or 80% of the time that the processing machine is operating wash the workpieces, we are aiming to increase the efficiency even for machines for high-variety products.
The interview having ended, here are the impressions of Tokyo Seimitsu...
From the talk about aircraft control systems, to the topic in recent years of collaborative robots, I have heard very thought-provoking words. I have gained a lot by hearing opinions directly from customers, such as the hope of standardization of programs that are different depending on the measurement instrument manufacturer. It is quite a difficult problem, but I believe we can improve bit by bit toward the construction of a new solution.
Tokyo Seimitsu listens to the customer’s requests, always aims to make better products, and desires to be a trusted manufacturer of choice. We will do our best to be able to provide useful products and services like Tamagawa Microtep.
Products