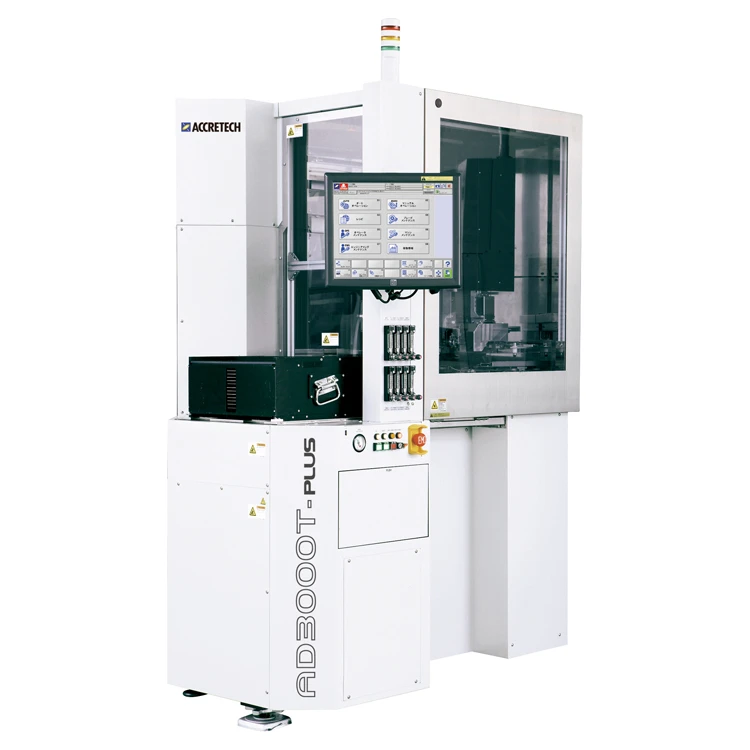
AD3000T-PLUS
The opposing type 2-axis spindles are arranged diagonally, to achieve both a reduced space design and high maintainability.
All daily operations such as blade replacement and maintenance work can be performed using front access from the front of the device. Access from the side is not necessary, so equipment layout is possible with small gaps. This contributes to labor-saving in clean rooms.
Features
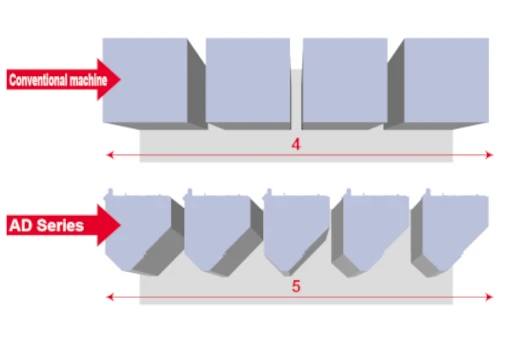
・Reduced space design
This is an originally developed diagonal layout design. Everything from normal operation to maintenance is accessible from the front.
When multiple units are installed in a line, since the lateral surface maintenance area can be reduced, 5 units of the AD3000T-PLUS can be installed in the installation space for 4 units of the conventional devices.
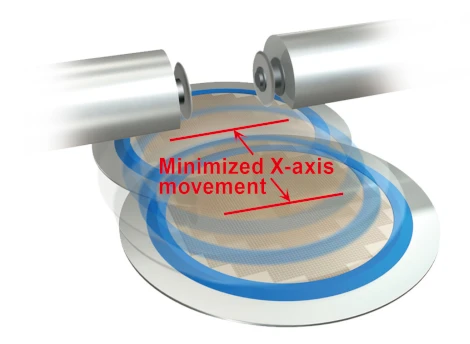
・Enhanced productivity (throughput)
Waste-free processing is achieved with an opposing type 2-axis spindle design and the minimum required X movement.
X axis speed: 1,000 mm/sec, Y axis speed: 300 mm/sec, Z axis speed: 80 mm/sec
Servomotors are used for all the X, Y, Z axes to speed up the axis speed
A reduction in processing time is achieved through optimization of the control software + synchronous control of the 3 axes
Two optical cutter-set (common name: OPC) units are mounted as standard. Reduction of the standby time by simultaneous set-up
・High-performance, high-output spindle equipped as standard
1.8 kW rating, maximum rotation speed of 60 krpm (a 2.2 kW rating, high-torque spindle can also be mounted as an option)
Processing of a wide range of materials is supported, from silicon to difficult-to-cut materials.
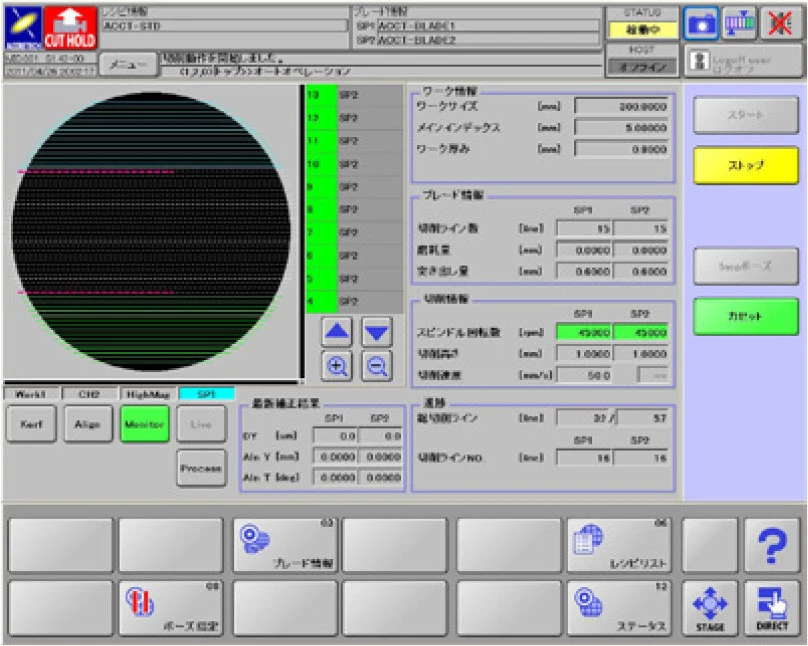
・Operability
A 17-inch touch panel + GUI (Graphical User Interface) are used.
Simply by touching the iconized buttons, straightforward and comfortable operation is achieved.
・Plenty of optional settings
Intermediate dress feature, built-in UV irradiation system, barcode reader automatic recipe switching feature, ionizer, etc.
The major optional units can be built-in due to the smaller footprint of the optional units and the optimized internal design
・Over 10000 recipes storable in the HDD
・USB port equipped as standard
(USB memory can be used as an external memory device)
・An echo function equipped as standard
With the optimization of the vacuum control, the amount of air consumption is reduced by 50% or more compared to our conventional devices.
Specifications
Maximum work size | Φ 305 mm | |
Maximum supported frame | 12 inch (SEMI G74-0699) | |
Spindle | Number of rotations | 60,000 rpm |
Maximum blade diameter | Φ 60 mm (2-Inch) Φ 80 mm (3-Inch) (option supported) |
|
Rating output | 1.8 KW | |
X axis | Cuttable range | 310 mm |
Fastest speed | 1,000 mm/s | |
Y1/Y2 axis | Cuttable range | 310 mm |
Fastest speed | 300 mm/s | |
Control resolution | 0.078 µm | |
Cumulative precision | 0.002 mm / 310 mm | |
Z1/Z2 axis | Stroke | 35 mm |
Resolution | 0.002 µm | |
Fastest speed | 80 mm/sec | |
Repeatability | 0.001 mm | |
Θ axis | Rotation range | 380° |
Specifications | Voltage | 3 Phase AC200 to 220 V ±10% (Other than the above, compatible with a transformer) |
Consumed electric power | 6.0 kVA (MAX) | |
Air supply pressure | 0.55 to 0.7 MPa | |
Average consumed volume of air | 210 L/min (at 0.55 MPa) | |
Average consumed volume of clean air | 140 L/min | |
Supply water pressure (cutting water, other) | 0.3 to 0.5 MPa | |
Supply water Maximum flow rate |
Cutting water: 10.0 L/min Water curtain: 3.0 L/min Other: 0.6 L/min |
|
Cooling water pressure | 0.3 to 0.5 MPa | |
Cooling water flow rate | 3.4 L/min (at 0.3 MPa) | |
Exhaust flow rate | 5.0 m³/min or greater | |
Dimensions (W x D x H) | 1,290 mm x 1,530 mm x 1,900 mm | |
Weight | 1,360 kg |
Automatic Blade Replacement Feature (Optional)
ABES (Auto Blade Exchange System)
In recent years, as part of factory automation, the introduction of automation into semiconductor back-end processing is progressing. The Φ 300 mm line in particular, from the viewpoint of them being unmanned and highly efficient, has an increase in activity to introduce automation. And, in the AD3000T-PLUS, in order to meet those demands, it is now possible to mount an automatic blade replacement system (Auto Blade Exchange System: ABES). In this system, the end of life of the HUB blade is automatically detected, from the HUB blade replacement to the return to processing is completely automated, and so the equipment downtime is minimized. In addition, depending on the individual operation status, the flange condition control feature, and the automatic adjustment feature of the blade damage detector can be mounted as options.
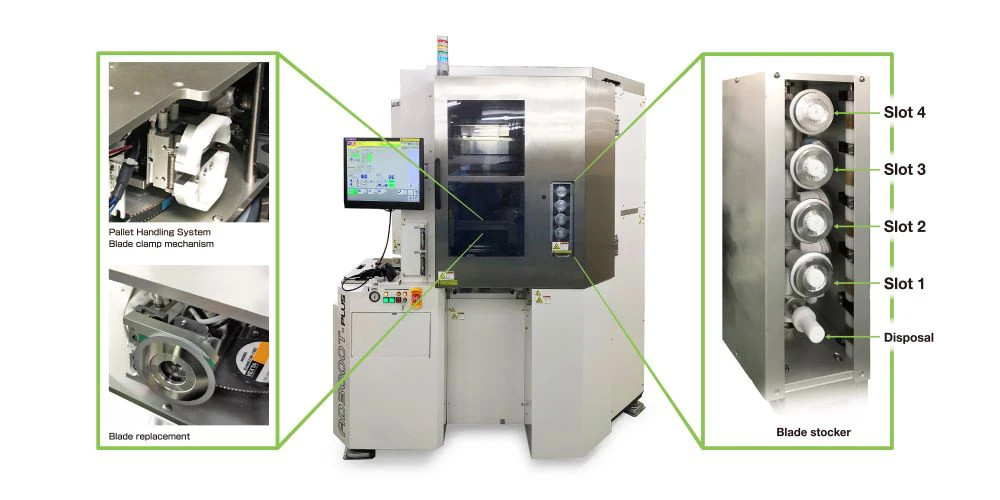
Maintenance
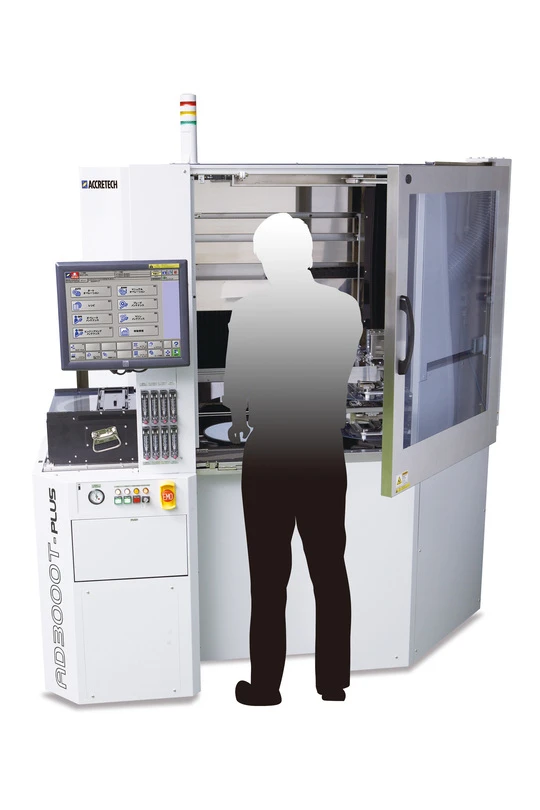
The maintainability is improved through the large door and large processing room.